Sensores de esfuerzo en materiales compuestos aeronáuticos
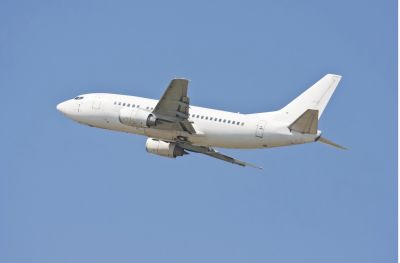
Strain sensors in aircraft composites
Los compuestos poliméricos han reemplazado progresivamente a las estructuras metálicas en la industria aeroespacial. Un grupo de científicos ha demostrado la viabilidad de integrar sensores de esfuerzo para conseguir una vigilancia continua de la integridad estructural y mejoras importantes en seguridad.
Los compuestos ofrecen una resistencia excelente con un peso reducido,
aspecto este último que contribuye a reducir las emisiones y el consumo
de combustible. Las estructuras de emparedado se han convertido en la
elección preferida para obtener diseños ligeros y robustos. Un tipo de
espuma espesa y de baja densidad forma el núcleo alrededor del cual se
adhieren elementos superficiales planos finos pero robustos.
Los núcleos de espuma ROHACELL producidos por EVONIK ROHM GMBH se utilizan ampliamente en el sector aeroespacial. Las espumas de láminas alveolares están formadas por una variedad de polímeros y elementos planos o capas de revestimiento normalmente de plástico reforzado con fibra de carbono (PRFC). La empresa puso en marcha el proyecto SANDWICH FOAM CORES, financiado con fondos europeos, con el propósito de diseñar y fabricar estructuras de emparedado PRFC con sensores integrados para vigilancia de la salud estructural (SHM).
La SHM, herramienta fundamental en la mejora de la seguridad y la fiabilidad de las estructuras críticas, podría con su integración reducir simultáneamente los costes y el tiempo asociados al mantenimiento. Los sensores pequeños y simples de fibra con rejilla de Bragg (FBG) son una opción excelente para vigilar los PRFC sometidos a gran tensión en las aeronaves.
Las FBG están fabricadas de un segmento corto de fibra óptica que transmite longitudes de onda específicas, las cuales varían a consecuencia de los esfuerzos y dar lugar a un sensor de esfuerzo. Además, las FBG no necesitan alimentación externa, son inmunes a la interferencia electromagnética, incluidos los relámpagos, resultan idóneas para operar a muy baja temperatura y han demostrado una buena resistencia a la corrosión y estabilidad a largo plazo.
El equipo científico diseñó y fabricó innovadores núcleos de espuma ROHACELL. En el autoclave se produjeron las partes curadas del demostrador, las cuales constaban de camisas endurecidas rellenas con núcleos de espuma y sensores FBG integrados. El proyecto SANDWICH FOAM CORES demostró un rendimiento adecuado del sensor FBG en las partes curadas del demostrador, lo que confirma la viabilidad de integrar sistemas SHM en las estructuras de emparedado a base de compuestos.
Se seguirá trabajando a fin de avanzar en el desarrollo de normas de diseño especiales para este tipo de componentes. La comercialización de estos materiales y procesos reforzará considerablemente la competitividad de la industria aeroespacial de la Unión Europea. La mejora de la seguridad, la disminución de costes y la reducción de emisiones asociadas a los viajes podrían también resultar muy beneficiosas para otros medios de transporte.
publicado: 2015-06-26